Commercial
How automation is transforming industrial property
Published
24 July, 2018
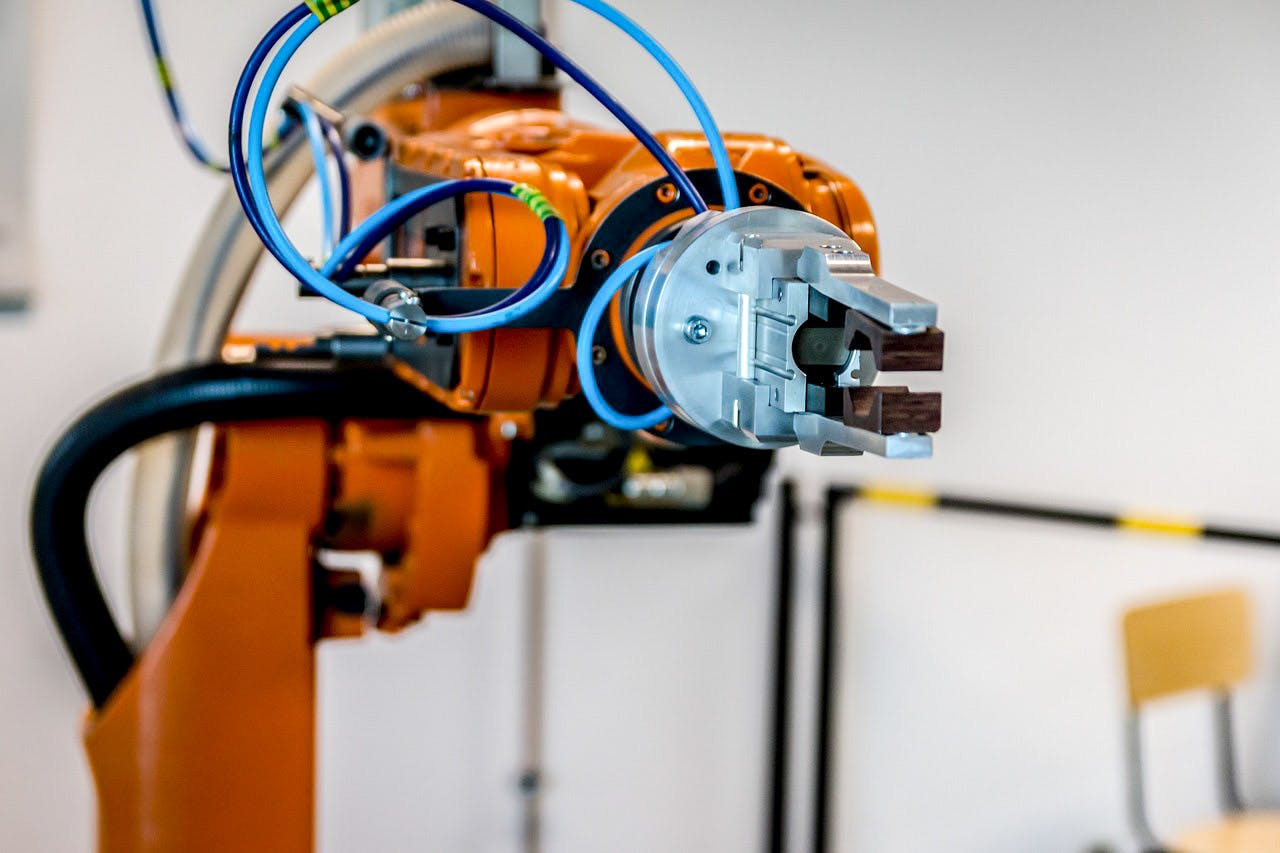
We talk of battery-operated cars flooding our roads and read about their impact on oil company and government profits. News of Amazon’s encroachment on Australian soil has caused stirring news headlines and pushed traditional retailers to lift their game (or tremble in online-bought boots). And digitised practices have scarily retrenched many white-collar employees from major banks and organisations.
But how is a wave of technology advances impacting the industrial sector? After all, industry contributes to a quarter of our national GDP. And what are warehouse and factory users, manufacturers and landlords doing about it?
The keyword is automation. And it’s seeing the rollout of another industrial revolution.
What is Automation?
Automated practices remove the need for many human-based functions in the workplace. It might be software to eliminate manual stocktaking or robots to substitute manual labourers.
This AI revolution has even impacted Australian banks, which are saying that for 60 per cent of jobs, 30 per cent of the activities are automatable. The impact could be greater for the industrial logistics and warehousing sector.
Traditional manual warehouses are defined as “person-to-goods” warehouses. In distribution centres, for example, the picking process is simple. A worker will move to a pick location, pick an item from the floor with a trolley, and deliver the goods to a delivery dock. Some mechanical functions may be involved (i.e. forklifts and conveyors) but for the most part workers are the key operators.
In comparison, automated warehouses perform these functions almost unconsciously and with little human interaction. When orders are made, a robot will handle materials and deliver them directly to the appropriate workers using sortation equipment and Automated Storage and Retrieval Systems (AS/AR).
Automated warehouses are defined as “goods-to-person”.
The differences in output are startling.
A manual warehouse will need 40 to 50 pickers (i.e. trolleys or workers) to process around 20,000 orders per hour. An automated warehouse using robots or shuttles will do the same work with only one to five pickers.
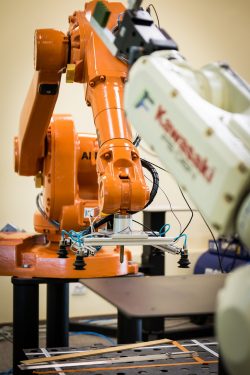
One robot in an automated warehouse will have the same output as 40 to 50 workers in a traditional warehouse.
Industry demands are changing
For manufacturers, increasing productivity is no doubt appealing. But another spark in the automation fire has come from the retail sector.
An increase in online shopping has translated to a surge in warehousing and distribution premise requirements.
With Amazon soon to be leading the charge for e-commerce in Australia it’s common sense to think about where they will store goods. Two fulfilment centres located on the eastern seaboard will service all of Amazon Australia’s online shoppers and have the potential to be the nation’s virtual Santa Clause come holiday season. This is just one (albeit enormous) company though.
We’re seeing supermarkets use robots like chess pieces to move, lift and sort through millions of grocery items each week. And as online shopping is growing at a rate of 10.2% per year in Australia, it’s not shocking that courier services have become vital.
Take Toll, for example. The logistics giant has recently moved into a new $160 million distribution centre in Prestons, Western Sydney. The new centre will be able to pick about 35,000 orders in an hour and have boxes ready for shipment within 30 minutes.
How does the warehouse function? Completely automated of course. Contemporary customer demand is for convenience and efficiency.
What this means for industrial businesses…
Not every industrial premises has the ability to accommodate automation. In fact, most in Australia probably don’t fit the requirements for powerhouses like Amazon, Toll and Costco.
“The majority of Australian warehouses and supply chain systems are outdated or not properly suited to the rapidly changing Australian retail, transport and infrastructure landscape”, says Travis Erridge, co-founder of supply chain consultancy TM Insight.
When speaking with the AFR, Mr Erridge compared Australia’s lagging growth of smart technologies to the US’s well-established automation industry (in the States, over 70 per cent of all new major warehouses are automated). But we are tipped to close the gap.
“There has been a significant shift in automation or semi-automated facilities driving the major distribution centres in Australia, particularly high bay warehousing. Even small companies are now starting to invest in automation through financing or in some cases developer incentives,” Mr Erridge says.
Our nation isn’t a tech hub, yet. Technology advances are trending on our shores, and with labour costs so high it is expected automation will continue to whet many business’s appetites. Plus, research points to falling robot prices in comparison with labour costs.
In summary: ‘watch this space’.
What this means for industrial property…
So, how might automation impact industrial property in Australia?
Well, while the industrial sector hasn’t yet drawn up plans to remove any and all of its human touch points, certain businesses understand the need to eliminate some of them.
This means industrial premises are likely to evolve to allow for at least some automation of warehousing (automated stacking cranes and transfer systems).
Automated equipment may be expensive and may certainly be considered specialised for particular businesses. But they will more than likely grow to become the norm for many operators – much the same as battery operated cars for the average driver and e-commerce for the average shopper.
Retail environment changes, automotive upheavals and white-collar redundancies should be a tap on the shoulder to warehousing and logistics businesses – and their landlords.
While the path to complete automation is a long one, we are heading toward more robot-centric sectors of the economy. It won’t be a surprise that more property investors will begin considering this when purchasing industrial real estate.
Properties & Pathways is a dynamic commercial property investment firm in Australia. We manage a boutique, high-yielding portfolio and have enjoyed 82% average annual portfolio growth alongside our investors since inception. For more information, get in touch with us or join our mailing list.